In my last post, I discussed how Garrett turbos are named, and briefly touched on some of the major differences between the different types of turbos. I wanted to talk more about some of the newer turbo technologies and some of the products we’ve been working on at CZP. Perhaps the most interesting thing on Garrett’s lineup right now is the GTX series. This is Garrett’s latest generation turbocharger, it’s their answer to the BorgWarner EFR turbo. While it’s very similar to the older GT style turbos, there are a few major differences.
- Billet compressor wheels. Instead of casting the compressor wheels, they are milled from a single piece of aluminum. Billet construction allows for several changes to be made in the compressor wheel…
- Thinner root on the compressor wheel, which allows for greater blade surface area
- Taller root on the compressor wheel, which allows for greater blade surface area
- Extended blade tips that reach further into the compressor housing, for greater blade surface area (notice the trend?
Those are the only differences in the CHRAs. Basically, the goal was to make a more modern compressor wheel which can move more air without adding to the amount of rotating mass. This means that, for the same RPM, a GTX compressor wheel will move more air than a comparable “GT” compressor wheel. So you reach your target boost pressure faster, with the potential for higher horsepower.
Additionally, the official Garrett GTX compressor wheels have switched over to an 11 blade design, wherein all 11 blades are full size. This is generally favorable for applications with a large, single turbo setup, but when implemented on smaller turbos in tends to produce more inconsistent boost, with a bit of an initial spike, followed by a declining taper to the boost pressure. For this reason, most smaller Garrett turbos use what’s called a 6×6 design, where you have 6 full-sized blades with 6 “sub” blades in between, which tends to produce more linear boost in smaller applications, like those used on the 300ZX.
GTX turbos also feature “anti-surge” ports on their compressor housings, to help combat this. In the real world, these aren’t necessary on the 300ZX, because you have ~12 feet of intake piping between the filter and the compressor, so even cars with breather mods generally don’t exhibit boost spiking issues. Of course, this changes once you go with really, really large turbos, but is generally not an issue.
To add to the situation, Garrett simply doesn’t offer a GTX turbocharger in many variants, the GTX2860R essentially being the smallest. Clearly, the GTX series was made with larger, single-turbo applications in mind.
So, Turbos Direct introduced the Pro-Boosted series of turbochargers. Turbos Direct is one of the few authorized Garrett dealers in the US. We’re lucky to have them in our own back yard, and we’ve worked with them for several years for building and rebuilding Garrett turbochargers. These are essentially filling in the gaps where Garrett left off, bringing the improvements introduced with the GTX turbo to other models where appropriate. These are a blend of GT and GTX style compressor wheels. For example, the compressor wheels all use billet construction, and as such they adopt the thinner root, longer/taller blades, and extended tips. However, they retain the 6×6 design which is favorable for smaller turbos, and do not implement the anti-surge turbine housing.
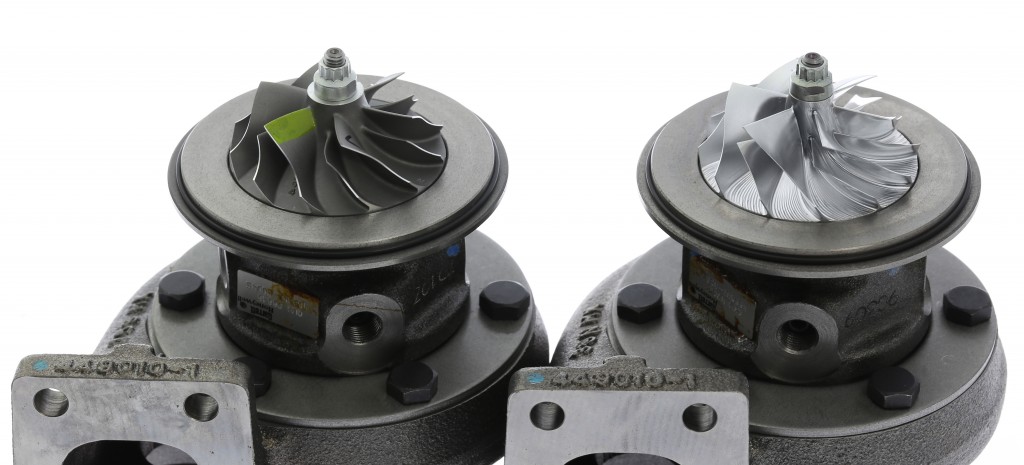
Left: Standard GT2560R compressor wheel. Right: Pro-Boosted version of the same wheel. Note how the center root of the turbo is much thinner on the billet version, creating blades with larger surface area.
When we talk specifically about the GT2560R compared to the billet version, the root is 3.8mm thinner, 1.5mm taller, and each main blade is 1.9mm longer. Like the GTX turbos, this yields a greater surface area, without changing the overall size of the compressor wheel, so it’s no laggier than a GT2560R, it just moves more air. Turbos Direct claims their Pro-Boosted version net a 15-20% increase in power over the standard versions.
Once the compressor wheel is switched over on the CHRA, the turbo is rebalanced. As a turbocharger often spins in excess of 150,000 RPM, it is absolutely essential that the assembly is perfectly balanced. You can see evidence of this balancing as slight machining done in the turbine (and sometimes also performed on the underside of the compressor wheel).
Once the turbo is balance and ready, it must be modified slightly to fit the 300ZX. This consists of removing the standard Garrett actuators, reclocking the turbos, adding inlet and outlet adapters, custom wastegate actuator brackets, and more compact Garrett (or Forge) actuators. There is also a post on the front of the compressor housing that must be machined down, and the outlet flange must be modified slightly on what will become the driver’s side turbo.
We use a custom jig to clock the turbochargers, which allows us to make sure the clocking is 100% accurate every time.
Then we add our custom inlet adapters. Care should be taken when installing these to make the transition between the adapter and compressor housing as seamless as possible. Simply alternating between the two bolts while tightening them does the trick. Our bolt-on adapters slightly limit the number of aftermarket intake pipes that work with the kit, but it produces a much more durable mounting solution and tighter seal than the “press on” adapters we’ve seen from some companies.
Then the turbo outlet needs to be added. These turbo outlets are 1.75″, which is actually just slightly larger than the size of the outlet of the compressor housing. But, since it’s a more standard size, it makes it much easier to source silicone couplers that fit.
Next, our custom wastegate actuator bracket is added, along with the more compact ~14psi Garrett actuators.
The Garrett actuators are just the actuators by themselves, so we need to add hardware to create a full adjustable wastegate arm. When sizing the arm, I like to let a “crescent” of wastegate lever show through, to emulate the amount of tension stock turbos use.
Once it’s installed, everything can be tightened down with a small amount of loctite to ensure nothing will slip after the turbos are installed in the car, with the wastegate arms almost completely out of reach.
And there you have a completely assembled turbo, ready to be installed in a 300ZX!
It would be nice to see the Turbos Direct compressor wheels applied to stock turbos, JWT 530/550s , JWT 700 and HKS 2530s. A fully modded 500whp stock turbo car is a blast to drive, I would love to see results with a new generation compressor wheels applied to stock turbos and the other small frame turbos for z32.
-Dane